Selective Seam Weld Corrosion -
How Big is the Problem?
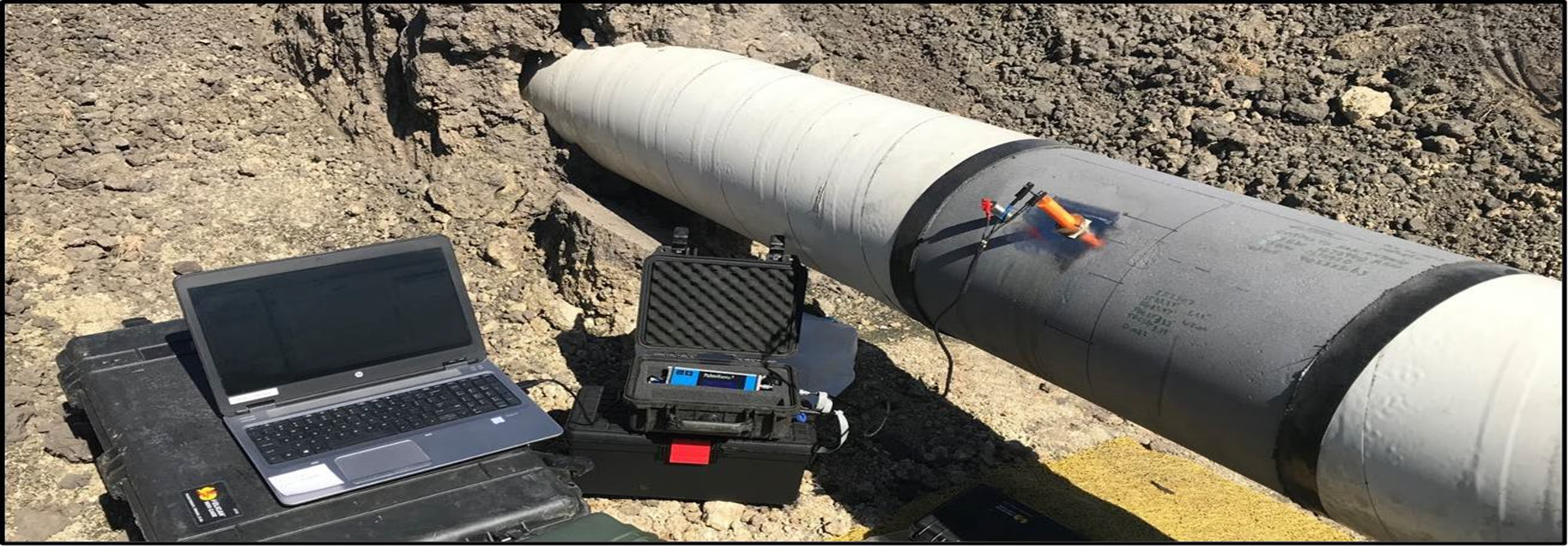
Table of Contents:
- What Is Selective Seam Weld Corrosion?
- Analysis of DOT Reportable Incidents
- Integrity Implications of SSWC
- Managing the Threat from Selective Seam Weld Corrosion
What is Selective Seam Weld Corrosion?
Selective Seam Weld Corrosion (SSWC) is a type of corrosion that affects the bondline region and heat-affected zone (HAZ) of the longitudinal seam of a pipeline forming grooves in the seam. The term “selective” refers to the preferential attack of the weld zone rather than the adjacent base metal. SSWC can be internal or external and has been reported in gas and liquid pipelines. This type of corrosion has been observed mostly in older vintage pipes, particularly those manufactured prior to 1970 and manufactured using direct-current electric resistance welding (DC-ERW), low-frequency electric resistance welding (LF-ERW), and flash welding. Figure 1 shows metallographic sections of some welds affected by SSWC.
The fact that SSWC is prevalent in seams produced in a particular era under similar coating and CP conditions suggests that it is driven not only by classic corrosion mechanisms but also by the properties of the seam material, which renders it more susceptible to this threat. This implies that SSWC is a threat interaction between a “corrosion mechanism” and a “defective pipe seam.” Integrity management principles require that the operator consider integrity threat interaction. Where a lack of effective corrosion control exists simultaneously with a susceptible seam, the likelihood of failure is significantly greater. Therefore, any strategy developed to identify the presence, susceptibility, and mitigation of SSWC threats must address these two important causative factors.
Analysis of DOT Reportable Incidents
It is important to understand the significance of this threat in the broader context of other pipeline threats. A useful way to evaluate this is to examine the relative number of incidents caused by this threat relative to other known interacting threats. The Pipeline Hazardous Material Safety Administration (PHMSA) reportable incident database contains the United States’ failure data for liquid and gas pipelines. [5] In 2016, Kiefner completed a research study for PHMSA to enhance understanding of interacting threats to pipeline integrity and minimize the risk of incidents from threat interactions. This study examined incidents reported to PHMSA that were caused by interacting threat situations recognized in ASME B31.8S, API 1160, as well as other industry literature. 4, Kiefner reviewed 8, 468 incidents in hazardous liquid pipelines recorded from 1986 to 2015, out of which 527 incidents (approximately 6%), were attributed to interacting threats. Two thousand seven hundred and sixteen incidents in gas pipelines documented during the period between 1985 and 2015 were also reviewed; of these, 306 incidents, approximately 12%, involved threat interactions. The figure below shows 16 of the 23 identified threat interactions, including SSWC, responsible for most (over 75%) of the releases documented in PHMSA’s incident database.
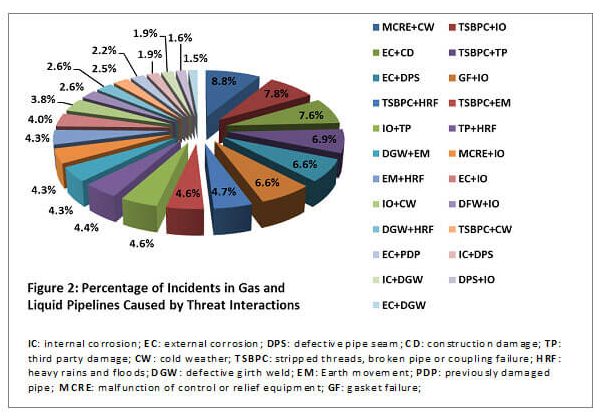
Integrity Implications of SSWC
The interacting nature of SSWC threat presents an elevated risk for several reasons: a) the localized corrosion typically occurs at a faster rate, of between 2 to 4 times the rate on the base metal (or pipe body); b) pipe seams produced by DC- and LF-ERW generally tend to exhibit low toughness, which could potentially lead to failure at lower stress levels; c) failure in low toughness seams, which is characteristic of DC- and LF-ERW seams, could result in a rupture; d) SSWC could interact with stable manufacturing seam flaws, such as lack of fusion to cause a failure where one would otherwise not have occurred in the absence of the SSWC; and e) SSWC features are axially oriented and may be difficult to find with a conventional magnetic flux leakage (MFL) tool and, where detected, may be difficult to characterize.
While the grooves caused by SSWC are not as narrow as the separation planes of actual cracks, they may be narrow enough (crack-like) to produce similar integrity effects.
Managing the Threat from Selective Seam Weld Corrosion
Strategies for managing an SSWC threat will be discussed in a subsequent blog. However, a brief comment regarding the management of this threat is useful. Industry standards like API 1160 provide useful guidelines for managing SSWC threats. The first step to controlling an SSWC threat is to determine whether your pipeline asset could potentially contain pipe seams that could be susceptible to it. This is consistent with new regulations that promote early identification and repair. [6] Where underlying data support potential susceptibility, the operator may need to conduct field investigations or laboratory tests on pipe samples to verify the presence of SSWC. Some of these tests may need to be conducted opportunistically when a section of the pipeline is excavated for in-situ integrity verifications or where pipe joints are removed from the pipeline for laboratory testing. Where there is evidence that SSWC exists or is suspected, a comprehensive strategy for mitigation will be required.
Kiefner has been involved in several leading industry studies that have provided a better understanding of the significance and control of this threat. Our experts have extensive experience supporting pipeline operators in developing strategies for determining their assets’ potential susceptibility to SSWC, conducting tests on pipe samples to evaluate the presence and significance of SSWC identified, and developing strategies for managing the integrity of pipelines susceptible to this threat.